Materiales ligeros para fabricar vehículos más sostenibles
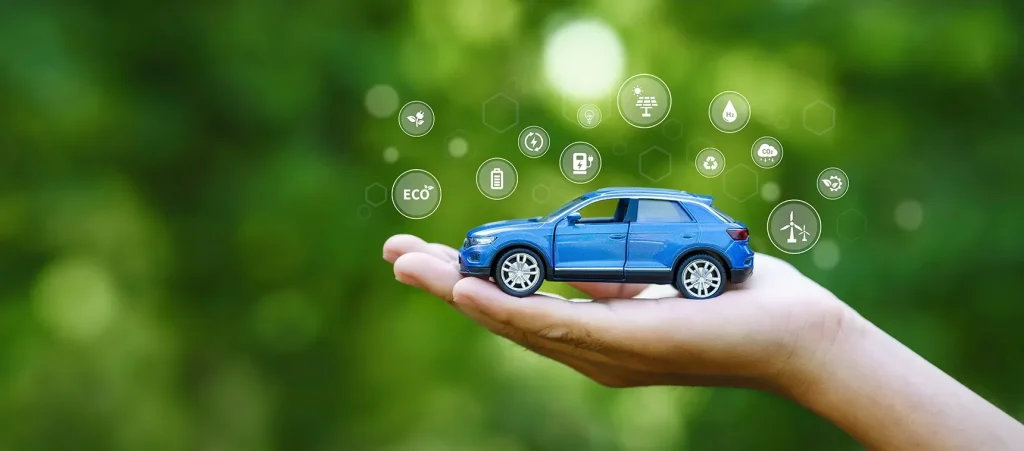
Beneficios que aportan los materiales ligeros en la fabricación de vehículos
La industria de la automoción se encuentra en una constante búsqueda de la eficiencia y la sostenibilidad. Esto ha llevado a un renovado interés en el uso de materiales ligeros para la fabricación de piezas y componentes que permiten producir coches más eficientes y más respetuosos con el medioambiente.
Estos materiales ofrecen una serie de ventajas significativas que impactan, tanto en el rendimiento del vehículo, como en su huella medioambiental. Veamos brevemente los beneficios que aporta el uso de estos materiales ligeros a la hora de fabricar vehículos más sostenibles.
Mejora de la eficiencia energética
El empleo de materiales ligeros en la fabricación de vehículos contribuye directamente a mejorar su eficiencia energética. Al reducir el peso total del vehículo, se requiere menos energía para impulsarlo, lo que se traduce en un menor consumo de combustible en vehículos con motores de combustión interna y una mayor autonomía en vehículos eléctricos.
Por ejemplo, cada 100 kg de reducción en el peso del vehículo puede mejorar la eficiencia del combustible en aproximadamente un 3-5%, dependiendo del tipo de vehículo y las condiciones de conducción.
Esta mejora en la eficiencia energética, no sólo reduce los costes asociados a los propietarios de los vehículos, sino que también disminuye las emisiones de gases de efecto invernadero y otros contaminantes, contribuyendo así a la mitigación del cambio climático y mejorando la calidad del aire en entornos urbanos.
Reducción de emisiones de CO2 y cumplimiento de normativas ambientales
El uso de materiales ligeros en la fabricación de vehículos también ayuda a los fabricantes a cumplir con las estrictas normativas medioambientales vigentes en todo el mundo. Las regulaciones, cada vez más exigentes, establecen determinados límites a las emisiones de CO2 y otros contaminantes, lo que obliga a los fabricantes a buscar soluciones innovadoras para reducir la huella ambiental de sus productos.

El empleo de materiales ligeros permite a los fabricantes diseñar vehículos más eficientes y menos contaminantes, asegurando así el cumplimiento de estas normativas y evitando sanciones y multas.
Beneficios adicionales: rendimiento, seguridad y costes
Además de los beneficios medioambientales y regulatorios, el uso de materiales ligeros también conlleva una serie de ventajas adicionales para los fabricantes y los consumidores. En términos de rendimiento, los vehículos construidos con materiales ligeros suelen tener una mejor aceleración y capacidad de frenado en comparación con los vehículos construidos con materiales más pesados. Esto redunda en la experiencia de conducción y la satisfacción del cliente.
En cuanto a la seguridad. muchos de los componentes ligados a los sistemas de seguridad pasiva de los automóviles, diseñados para proteger a los ocupantes en caso de accidente, se diseñan y fabrican utilizando materiales ligeros con excelentes propiedades en términos de resistencia ante impactos. Adicionalmente, la utilización de materiales ligeros produce ahorros significativos en los procesos logísticos (internos y externos) asociados al movimiento de productos semielaborados o elaborados.
Además, el uso de materiales ligeros también puede conducir a una reducción de los costes de fabricación a largo plazo, ya que se requieren menos materiales y recursos para producir vehículos más ligeros, lo que puede traducirse en ahorros significativos en los procesos de producción y ensamblaje.
Principales materiales ligeros utilizados en la fabricación de vehículos
Veamos a continuación algunos de los materiales ligeros más empleados en el sector de la automoción, así como sus propiedades y aplicaciones en la fabricación de vehículos.
1. Aluminio
Características y propiedades
El aluminio es un metal ligero con una serie de características y propiedades que lo hacen ideal para su uso en el ámbito de la movilidad en general (aeronáutica, ferrocarril…) y, especialmente, en la industria de la automoción. Una de las características más destacadas del aluminio es su elevado ratio entre su resistencia mecánica y su densidad, uno de los más elevados entre los metales disponibles comercialmente.
Además, el aluminio es altamente maleable y fácilmente moldeable, lo que permite a los fabricantes crear componentes y piezas de formas complejas con relativa facilidad, adaptándose a procesos productivos tan diferentes como el moldeo por inyección (a alta o baja presión), la estampación, la extrusión.
Otra propiedad importante del aluminio es su excelente resistencia a la corrosión y los bajos costes asociados a incrementar esta resistencia mediante recubrimientos (lacado, anodizado), lo que lo hace ideal para su uso en entornos exteriores y en aplicaciones donde se requiere resistencia a la intemperie y a los agentes químicos. En general, prácticamente todos los materiales metálicos son altamente reciclables pero esto es algo especialmente significativo en el aluminio
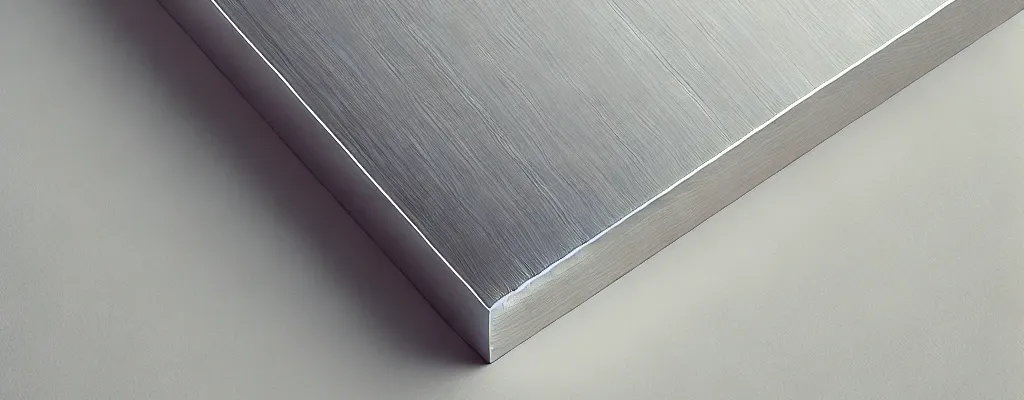
Aplicaciones para la fabricación de vehículos
Una de las aplicaciones más comunes del aluminio en la industria automoción es en la construcción de carrocerías y chasis. El uso de aluminio en estas áreas permite a los fabricantes reducir significativamente el peso total del vehículo, lo que se traduce en una mejor eficiencia energética, mayor rendimiento y menor consumo de combustible.
Además, el aluminio se utiliza en la fabricación de componentes internos y externos del vehículo, como paneles de carrocería, puertas, capós, y llantas, entre otros. En la actualidad es además un material ampliamente utilizado en soluciones multimateriales, dada la facilidad con la que puede unirse, incluso estructuralmente, a otros materiales ligeros (como los materiales compuestos). En resumen, el aluminio es un material versátil y eficiente, proporcionando una combinación única de ligereza, resistencia y durabilidad.
2. Aceros avanzados de alta resistencia (AHSS, Advanced High Strength Steels)
Características y propiedades
Los aceros avanzados de alta resistencia (AHSS, por sus siglas en inglés) ofrecen una alta resistencia a la tracción, permitiendo que los componentes soporten grandes esfuerzos sin comprometer su integridad estructural, algo crucial para la seguridad del vehículo. Además, a pesar de su alta resistencia, los AHSS mantienen una buena ductilidad, permitiendo que se deformen de manera controlada bajo carga.
Además, a pesar de su alta resistencia (que puede duplicar o triplicar la habitual en un acero convencional), estos materiales siguen mantienen la tradicional buena ductilidad de los aceros convencionales al carbono, permitiendo que se deformen de manera controlada bajo carga.
Esta propiedad es esencial para la absorción de impactos y la distribución de fuerzas durante un accidente. Los AHSS también permiten una reducción significativa del peso, ya que su alta relación resistencia / peso específico permite usar menos material para lograr la misma rigidez estructural que con los aceros tradicionales. Esto contribuye a una mejor eficiencia del uso de combustible y, por lo tanto, una reducción en las emisiones de CO2.
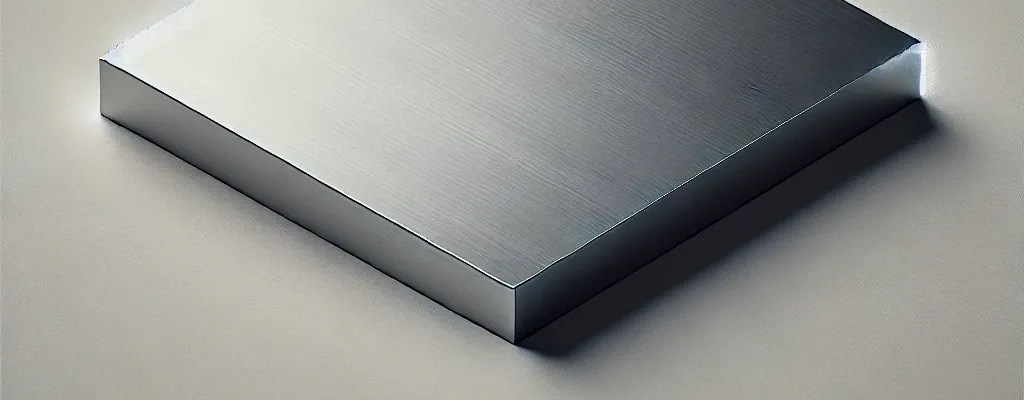
Aplicaciones para la fabricación de vehículos
En automoción, los aceros de alta resistencia se utilizan ampliamente en la construcción del chasis y otros componentes estructurales del vehículo. Además, estos aceros se emplean en zonas de impacto y otros componentes críticos de seguridad, como pilares y refuerzos laterales, ayudando a cumplir con los estándares de seguridad más estrictos, así como en paneles de carrocería con elevados requisitos estructurales y de conformabilidad.
En resumen, los aceros avanzados de alta resistencia son un componente clave en la fabricación de vehículos modernos, mejorando tanto la seguridad como la eficiencia, y ofreciendo ventajas medioambientales significativas
3. Aleaciones de magnesio
Características y propiedades
Las aleaciones metálicas de magnesio son otra buena opción si lo que se busca es un material ligero, con una gran relación resistencia-peso. Además de su ligereza y su excelente resistencia a la corrosión, estas aleaciones también destacan por tener una excelente conductividad térmica y eléctrica, así como un muy buen comportamiento a altas temperaturas. El magnesio es además un mineral ampliamente disponible en la naturaleza por lo que su coste y disponibilidad industrial es razonable.
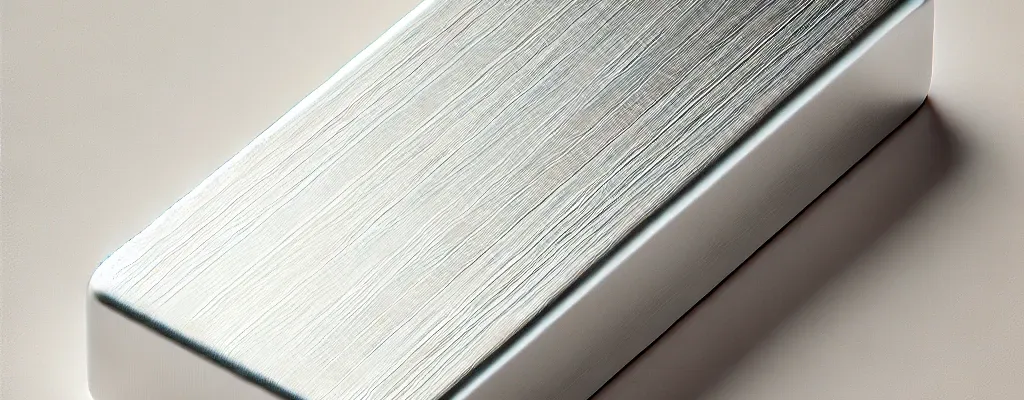
Aplicaciones para la fabricación de vehículos
Es muy empleado, sobre todo, en la fabricación de bloques motor, donde su ligereza y propiedades físico-químicas lo hacen muy competitivo si se quiere trabajar con motores más ligeros, más pequeños y sometidos a mayores esfuerzos que los tradicionales.
El auge del concepto denominado downsizing en el desarrollo de motores (disminuir su tamaño manteniendo la potencia) ha sido posible por la amplia utilización de este tipo de aleaciones. También se emplea en la fabricación de llantas y otros componentes estructurales del vehículo.
4. Materiales compuestos reforzados con fibras continuas
Características y propiedades
Los materiales compuestos reforzados con fibras continuas están formados por una matriz polimérica, termoplástica o termoestable, y un refuerzo en forma de fibras (unidireccionales o en formato de tejido uni, bi o incluso tridimensional) habitualmente de origen inorgánico: fibras de carbono y fibras de vidrio.
Una de las características más destacadas de estos materiales es su imbatible relación entre resistencia y peso específico, que los convierte en una alternativa ligera y robusta a los tradicionales materiales metálicos para la industria de la automoción. Cuenta, además, por su carácter de materiales “plásticos”, con un excelente comportamiento ante la corrosión e incluso la fatiga mecánica, lo que los hace ideales para su uso en aplicaciones donde se requiere una buena resistencia estructural y durabilidad a largo plazo.
Su principal desventaja frente a la utilización de los materiales metálicos que se han comentado con anterioridad es su menor rigidez (a igualdad de esfuerzo por unidad de área de trabajo, se deforman significativamente más) así como los habitualmente mayores costes asociados a su transformación en componentes en grandes series,
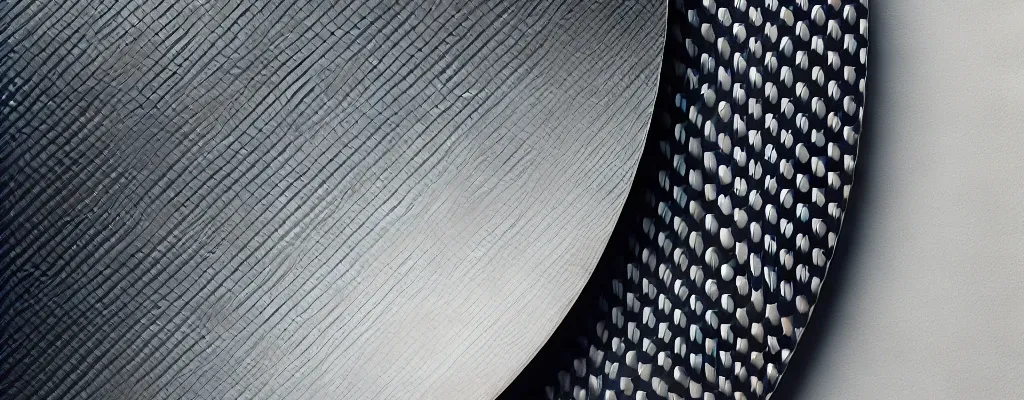
Aplicaciones para la fabricación de vehículos
Este material se está introduciendo de manera paulatina en la industria de la automoción gracias a sus sobresalientes propiedades mecánicas, su excelente resistencia a la fatiga y su evidente ligereza. Principalmente, se emplea en la producción de componentes estructurales, habitualmente combinado con aluminio, conformando componentes multimaterial.
Como se ha comentado con anterioridad, se está trabajando actualmente en procesos de fabricación que, manteniendo sus excelentes propiedades mecánicas y de resistencia ambiental, abaraten la producción de estos componentes a gran escala.
5. Materiales termoplásticos reforzados con fibras discontinuas (o fibras cortas)
Características y propiedades
Los termoplásticos reforzados con fibra corta son materiales que combinan una matriz termoplástica con materiales de refuerzo en forma de fibras cortas inorgánicas (vidrio, habitualmente) o, últimamente, orgánicas (refuerzos biobasados obtenidos de residuos agrícolas como el sisal). Estos materiales ofrecen una serie de características y propiedades que los hacen ideales para su uso en la industria de la automoción:
- Son ligeros.
- Razonablemente resistentes.
- De coste reducido.
- Altamente moldeables (especialmente, con procesos de fabricación que garantizan altas cadencias de producción).
- Y muy reciclables.
Pueden adaptarse a una amplia variedad de formas y diseños, lo que permite a los fabricantes crear componentes y piezas de formas complejas con relativa facilidad. Su gran desventaja en la actualidad, pese a su elevada recicblabilidad, es la dependencia que suponen aún hoy del petróleo en una economía moderna que trata cada vez más de desvincularse de esta materia prima. Para ello, se están desarrollando de manera muy intensa nuevas matrices poliméricas biobasadas y, por tanto, independizadas de la industria del petróleo.
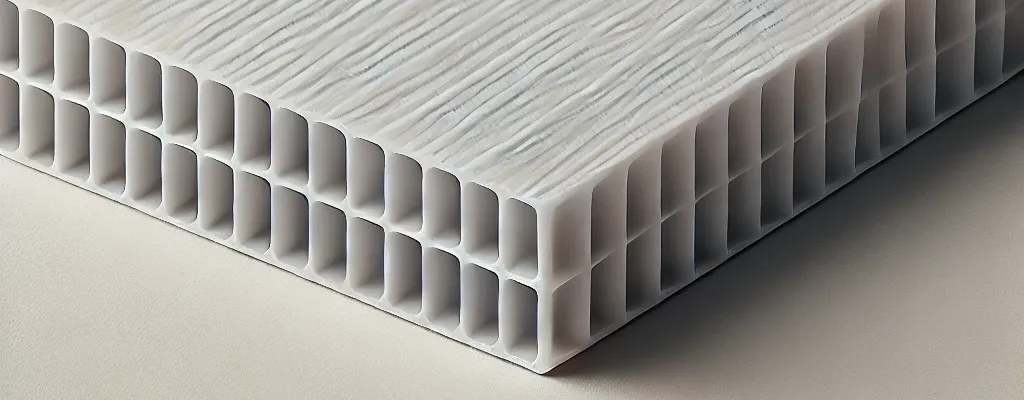
Aplicaciones para la fabricación de vehículos
Los termoplásticos reforzados con fibra corta se utilizan, habitualmente, en la producción de paneles de carrocería, parachoques, componentes estructurales y otras piezas del vehículo. Su ligereza y maleabilidad permite fabricar vehículos con una mayor eficiencia energética y una mejor maniobrabilidad. Además, ofrecen una excelente resistencia a la corrosión y a los impactos, lo que mejora la durabilidad y la seguridad del vehículo. En definitiva, este tipo de materiales ofrecen una gran combinación de ligereza, resistencia, durabilidad y coste.
6. Componentes multimaterial
Características y propiedades
Tal y como se ha comentado con anterioridad, cuando describíamos las características y uso del aluminio y los compuestos reforzados con fibra continua, los componentes multimaterial empiezan a incorporarse a la industria de la automoción y representan un innovador enfoque en la ingeniería de materiales, combinando diversas clases de materiales para optimizar las propiedades mecánicas, térmicas y eléctricas de los componentes.
Uno de las claves, cuando se trata de definir cómo interactuarán dos materiales de diferente naturaleza en un mismo componente, es el proceso con el que se mantienen unidos. Las uniones entre materiales disimilares, ya sean de tipo mecánico (soldadura, atornillado, remachado…) o químico (adhesivado, co-inyección, co-curado…) están siendo actualmente foco de multitud de trabajos y estudios, convirtiéndose en un importante vector de desarrollo tecnológico en el sector de la automoción.
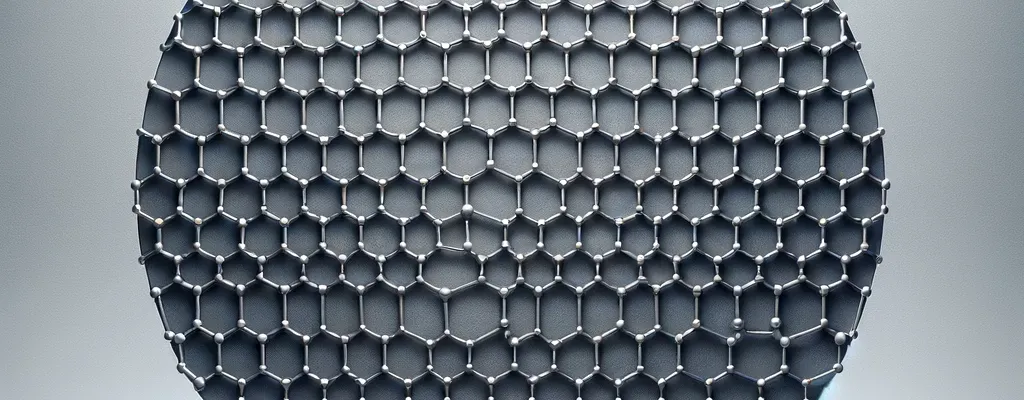
Aplicaciones para la fabricación de vehículos
En la industria de la automoción, las estructuras multimaterial están revolucionando el diseño y la fabricación de vehículos. Piezas de interior con inyecciones bimaterial, en los que dos materiales termoplásticos (habitualmente uno de ellos rígido y el otro flexible) ofrecen lo mejor de sus características para conseguir componentes multifuncionales, son habituales ya en los salpicaderos y otros guarnecidos interiores en los automóviles.
De igual manera, y a nivel estructural, empiezan a aparecer modelos de automóviles en los que el uso de aluminio y materiales compuestos reforzados con fibra larga conviven en brazos de torsión y en chasis. Esta tecnología, no sólo reduce el peso del vehículo, sino que también simplifica el diseño y mejora la estética y funcionalidad de los interiores del vehículo, consiguiendo resolver varias funciones en un único componente (materiales y componentes multifuncionales).
Presente, futuro y retos de los materiales ligeros en la movilidad sostenible
Ciclo de vida de los materiales ligeros y su reciclabilidad
La sostenibilidad de los materiales ligeros, no sólo se mide por su impacto en la eficiencia del combustible, sino también por su ciclo de vida y reciclabilidad. Materiales como el aluminio y los compuestos de plástico reforzado pueden ser reciclados de manera eficiente, reduciendo la necesidad de extraer y procesar nuevas materias primas. Diversos estudios de análisis de ciclo de vida demuestran que la huella medioambiental del aluminio lacado o anodizado reciclado es hasta un 40% menor que la del extraído virgen a partir de bauxita.
De igual manera, la introducción de materiales plásticos biobasados con refuerzos de fibra corta de origen orgánico supone un hito de gran importancia, tanto por su contribución a conseguir la neutralidad climática de la industria europea, como la independencia del petróleo de nuestra economía.
El reto tecnológico en torno a la fabricación de nuevos materiales biobasados es doble: por un lado, conseguir que estos materiales tengan propiedades mecánicas y de procesabilidad similares a los actuales termoplásticos con origen en el petróleo; y, por otro lado, garantizar una cadena de suministro estable para estos materiales biobasados que no afecte a las cadenas de valor alimentarias (humanas y animales).
Ejemplos de vehículos fabricados con materiales ligeros
Diversos fabricantes de automóviles han adoptado el uso de materiales ligeros en sus modelos más recientes, demostrando el impacto positivo en la sostenibilidad y el rendimiento. Un ejemplo notable es el BMW i3, que utiliza una estructura de fibra de carbono reforzada con plástico (CFRP), logrando un peso significativamente reducido y mejorando la eficiencia del vehículo eléctrico.
Otro caso es el Ford F-150, que ha incorporado una carrocería de aluminio de alta resistencia, resultando en una reducción de peso de 315 kgs comparado con sus predecesores de acero, mejorando, tanto la eficiencia del combustible, como el rendimiento general.
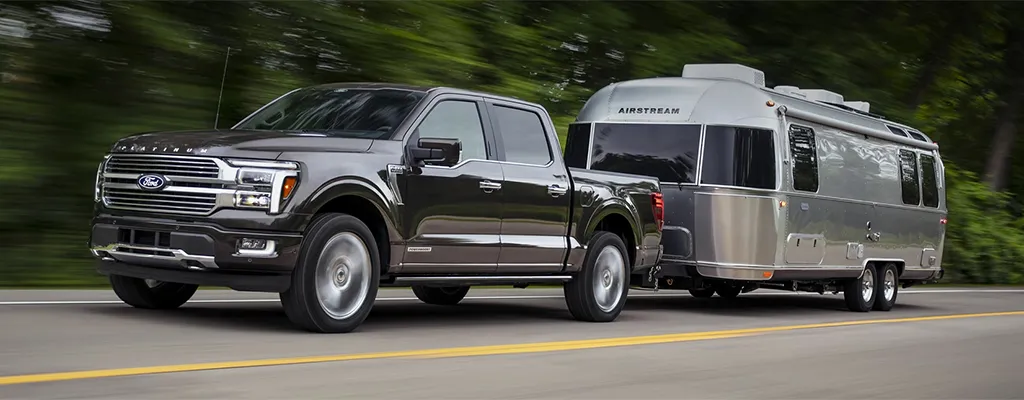
Además, todos los grandes fabricantes de automóviles a nivel europeo están incorporando ya en muchas de sus piezas de interior piezas de plástico reforzado con fibra corta reciclado y plásticos biobasados.
Estos ejemplos muestran cómo los materiales ligeros pueden ser integrados en la producción masiva de vehículos, mejorando la sostenibilidad y ofreciendo beneficios tangibles, tanto en términos de rendimiento, como desde un punto de vista económico y operativo.
Retos técnicos y de producción
La implementación de materiales ligeros en la industria de la automoción presenta varios desafíos técnicos y de producción. Uno de los principales retos es la dificultad en la manipulación y fabricación de estos materiales. Por ejemplo, la fibra de carbono requiere procesos de fabricación complejos y costosos, lo que puede limitar su adopción en la producción en masa.
Además, la unión de materiales disímiles, como aluminio y magnesio, puede presentar problemas técnicos debido a diferencias en sus propiedades físicas y químicas, requiriendo técnicas de soldadura y adhesión avanzadas. La integración de estos materiales en los procesos de producción existentes también puede implicar inversiones significativas en nuevas tecnologías y equipamiento, lo que puede ser un obstáculo para muchos fabricantes.
Perspectivas de futuro e innovación tecnológica
El futuro de los materiales ligeros en la movilidad sostenible es muy prometedor. La continua investigación y desarrollo están llevando a avances significativos en la producción y el uso de estos materiales. Por ejemplo, se están desarrollando nuevas técnicas de reciclaje para materiales compuestos de fibra de carbono, que podrían reducir significativamente los costes y el impacto ambiental de este material, tanto mediante técnicas químicas, como bio-encimáticas.
Además, los avances en la impresión 3D y la fabricación aditiva están abriendo nuevas posibilidades para la creación de componentes ligeros, complejos y multimaterial que no serían posibles con métodos de fabricación tradicionales.
El desarrollo de nuevos materiales avanzados también está impulsando el futuro de la movilidad sostenible. Materiales como los polímeros reforzados con grafeno y los nanocompuestos están mostrando un gran potencial para ofrecer propiedades superiores de resistencia y ligereza. Estos materiales, no sólo pueden mejorar el rendimiento y la eficiencia de los vehículos, sino que también pueden proporcionar beneficios adicionales como mayor durabilidad y resistencia a la corrosión.
La continua evolución de estos materiales promete transformar la industria de la automoción, haciendo que los vehículos sean no solo más ligeros y eficientes, sino también más sostenibles y ecológicos.
Soluciones ITA y casos de éxito
Aligeramiento de materiales
Desde el Instituto Tecnológico de Aragón, con el equipo de Materiales y Componentes al frente, contamos con una gran experiencia en el desarrollo de soluciones para el aligeramiento de materiales:
- Desarrollamos soluciones ligeras multimaterial para componentes estructurales: sustitución de soluciones convencionales de acero por metales ligeros (nuevos grados de acero y/o aluminio) combinados con composites (Plásticos Reforzados con Fibras – CFRP y/o GFRP).
- También realizamos la selección/fabricación/caracterización de materiales, diseño y cálculo estructural, análisis del proceso de fabricación, análisis del ciclo de vida, ensayos sobre prototipos.
- Soporte cálculo estructural (MEF) y ensayos en componentes/estructuras.
- Disponemos de una “Test & Experimentation Facility” de Materiales Compuestos, para que puedas desarrollar y prototipar de manera conjunta soluciones ligeras basadas en polímeros reforzados con fibra continua.
- Laboratorio de Ensayos Mecánicos, Integridad Estructural y Fatiga.
- Caracterización y modelización del comportamiento de materiales, integridad estructural y sistemas multimaterial y tecnologías de unión.
- Diseño y desarrollo de nuevos materiales ligeros multifuncionales a medida
- Desarrollo de tecnologías orientadas a la consecución del aligeramiento de estructuras haciendo un uso eficiente de los materiales y minimizando el consumo de energía en fabricación y uso. El aligeramiento estructural y la reducción de uso de material se pueden conseguir de varias formas:
- Sustitución de material.
- Optimización del diseño del componente/disposición (layout) del sistema.
- Innovación en el proceso de fabricación.
Soluciones avanzadas materiales compuestos
Uno de los campos en los que el ITA tiene mayor conocimiento es el desarrollo de materiales compuestos (composites) y uniones adhesivadas. Ofrecemos soluciones avanzadas para toda la cadena de valor de la industria de los composites:
- Diseño y desarrollo de materiales.
- Materiales computacionales.
- Caracterización de materiales.
- Gemelos digitales y modelado de transformación de procesos.
- Desarrollo de prototipos virtuales.
- Instalación de pruebas y experimentación en composites y juntas adhesivas.
- Laboratorio de pruebas de integridad estructural.
- Fin de vida y reciclaje.
Puedes consultar nuestro expertise en este campo haciendo click en la siguiente imagen:
Casos éxito
Contacta con nosotros
Déjanos tus datos de contacto si quieres que te ayudemos:
Artículo validado por:
Instituto Tecnológico de Aragón
ARTÍCULOS DEL MÍSMO ÁMBITO
-
Modelando una red de hidrógeno para un futuro más sostenible
Lunes, 09 Junio 2025
- Tecnologías del hidrógeno
-
Componentes del coche eléctrico: Desarrollo e implicaciones técnicas
Viernes, 24 Enero 2025
- Diseño y desarrollo de vehículos eficientes
OTROS ARTÍCULOS
-
Modelando una red de hidrógeno para un futuro más sostenible
Lunes, 09 Junio 2025
- Tecnologías del hidrógeno